Reducing Inventory to Uncover Hidden Inefficiencies in Your Supply Chain
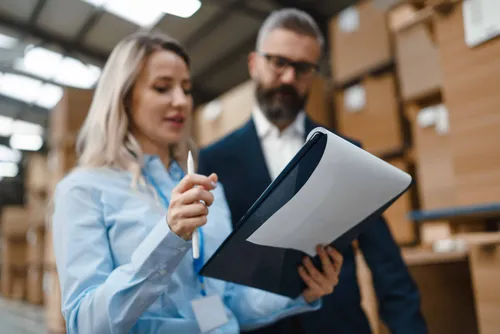
Costs, efficiency and service levels are key factors for business competitiveness. That’s why efficient inventory management has become an essential component of a successful supply chain strategy. Yet, many companies continue to hold excessive stock levels without questioning what inefficiencies might be concealed beneath the surface. In this context, the analogy of «lowering the water to see the rocks» offers a powerful perspective that challenges how we think about inventory and operational efficiency. Reducing inventory in a controlled way can be very useful to optimise inventory management.
In this blog post, we’ll explore what this concept involves, how to apply it safely, the benefits it can deliver, and why SCM software is essential to harness its full potential without unnecessary risks.
What Does “Lowering the Water” Mean in Inventory Management?
This visual and educational analogy compares inventory levels to the water level of a river. The more water there is, the harder it is to see the rocks beneath the surface. Translating this to inventory management: the higher the stock level, the less visible the problems and inefficiencies hidden underneath. These “rocks” could include quality issues, supplier delays, picking errors, outdated manual processes or a lack of coordination between departments.
When inventory is reduced, these inefficiencies become visible. What was previously cushioned by excess stock now surfaces clearly, forcing the company to address and resolve the issues. Rather than a risk, this exposure is an opportunity to drive continuous improvement.
Examples of Hidden Problems
Some of the most common problems hidden by high stock levels include:
- Frequent errors in warehouse inbound and outbound processes that were masked by surplus stock.
- Low delivery reliability from suppliers that went unnoticed due to buffer inventory.
- Poor product rotation, leading to obsolescence with no immediate visible impact.
- Quality issues that remained undetected thanks to available replacement units.
- Slow or inefficient picking and replenishment processes are often masked by excessive stock levels.
What’s the Goal Behind Reducing Inventory?
The purpose isn’t to cut stock arbitrarily, but to expose hidden weaknesses through a deliberate, gradual inventory reduction. It’s not an end in itself, but a means to detect inefficiencies and optimise the entire supply chain.
Reducing Inventory in a Controlled Way
Applying this approach means reducing stock levels carefully, supported by data analysis, key performance indicators and digital tools to minimise risk. It’s not about emptying warehouses but rather adjusting inventory to the point where system flaws begin to reveal themselves. Visibility and agility are critical to prevent stockouts or service level drops.
Revealing Structural Inefficiencies
As inventory is reduced, underlying issues become apparent, from errors in master data to inaccurate demand forecasts. This transparency allows companies to prioritise actions, allocate resources more effectively and develop improvement plans based on real information rather than assumptions.
Operational Benefits of This Strategy
When implemented intelligently, this strategy brings improvements across multiple areas. The benefits go far beyond logistics, impacting quality, planning and supplier relationships.
Boosting Operational Efficiency
By identifying bottlenecks and weak points, processes can be redesigned to be faster and more effective. From picking to replenishment, from demand planning to goods receipt, each step can be optimised using real data.
Cost Savings and Quality Improvements
Reducing inventory lowers storage needs, cuts the risk of obsolescence and frees up working capital. Moreover, by exposing errors and defects, businesses can address them and raise their overall quality standards.
Stronger Supplier Management
Once delays or non-compliance become visible, companies can renegotiate contracts, switch suppliers or introduce tighter control mechanisms directly improving supply chain reliability.
Case Study: TecnoAgro’s Transformation Through Reducing Inventory
To gain a clearer view how this concept works and what kind of improvements it can bring, let’s look at a fictional case study.
Initial Context: TecnoAgro in 2023
TecnoAgro, a distributor of agricultural machinery, operated with very high stock levels to ensure immediate availability. While this helped maintain good service levels, it also resulted in high logistics costs, poor stock turnover and inefficient management.
Implementation in 2024
In 2024, management decided to introduce an advanced inventory management system and progressively reduce stock levels. The strategy was supported by performance indicators and a digital solution to monitor every movement. Within months, previously hidden issues began to surface:
- Irregular deliveries from international suppliers.
- Faulty spare part batches.
- Mismatches between actual and recorded stock levels.
Corrective Measures
Once TecnoAgro identified the issues hidden beneath excess stock, they took action:
- Reviewed and renegotiated contracts with key suppliers.
- Introduced RFID technology and regular cycle audits.
- Relocated key items to more efficient warehouse zones.
- Improved master data management and demand forecasting.
Results Achieved
Following these actions, the company saw:
- A 38% reduction in storage costs.
- A 17% improvement in the service level for critical parts.
- A 21% drop in replenishment lead times.
- A decrease in return rates due to quality issues from 5.8% to 2.1%.
This approach enabled TecnoAgro not only to optimise inventory but also to strengthen supplier relationships, improve service quality and boost overall competitiveness.
How SCM Software Supports This Strategy
Reducing inventory without the right digital tools is risky. A dedicated SCM system provides the support needed to implement this approach safely, effectively and in a controlled manner.
Real-Time Visibility of Stock and Demand
With integration across purchasing, sales and warehouse systems, Supply Chain Management software offers a consolidated and real-time view of inventory. This enables informed decisions, stockout prevention and replenishment aligned with actual demand.
Automation and Smart Replenishment
Replenishment algorithms adjust to demand variability, historical consumption patterns and supplier conditions. This reduces the risk of human error, avoids unnecessary overstocking and ensures optimal stock levels per item.
Quality Control, Traceability and Compliance
A robust SCM system logs incidents, tracks each batch and produces automatic reports to support regulatory compliance. This is particularly crucial in sectors like pharmaceuticals, food or automotive, where errors can have serious consequences.
Reducing Inventory as a Strategy for Visibility, Control and Optimisation
This approach isn’t just another inventory reduction technique; it’s a mindset of continuous improvement rooted in transparency and critical analysis. When applied wisely, it helps organisations uncover weaknesses, enhance processes and build a more efficient, resilient and sustainable supply chain.
To make this strategy viable and secure, the right technology is essential. SCM software doesn’t just support the transition it turns it into a sustainable competitive advantage.
At Imperia, we offer supply chain optimisation software that helps businesses digitise and enhance every operational process. Our modular solution adapts to the specific needs of each company and sector, delivering only the functionality you truly need. If you’d like to find out how we can help, request a free consultation with one of our experts. We look forward to speaking with you!
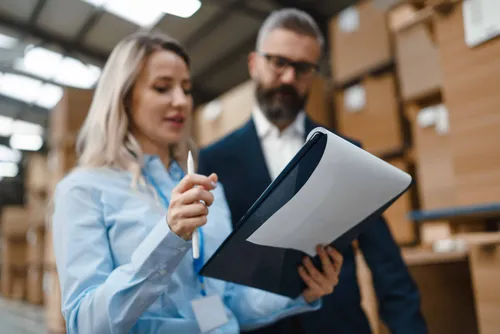
Subscribe to our newsletter and transform your management!
Receive updates and valuable resources that will help you optimise your purchasing and procurement process.