Finite Capacity vs. Infinite Capacity: Which Approach to Use in Your Production Planning
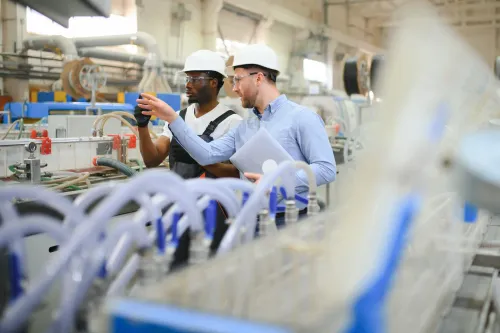
Planning production without considering the reality of your resources is one of the most common causes of non-compliance, bottlenecks, and operational deviations. Many companies still create plans based on infinite capacity, assuming that machines and personnel can respond without limitations. On the other hand, some have moved towards finite capacity planning, which considers the actual availability of resources and enables feasible decision-making.
But which approach is best for your company? Should you use finite or infinite capacity planning? In this post, we delve into both models, their differences, consequences, and how SCM software can help you adopt a plan aligned with your actual capacity.
What is Infinite Capacity and Why Was it the Standard for Years?
Infinite capacity planning assumes that productive resources (machines, people, facilities) can absorb any workload without limitations. In this model, the planner inputs demand, and the system generates a production plan without verifying whether there is enough time, machine capacity, or personnel to fulfil it.
For many years, this methodology was widely used for a simple reason: it’s quick to implement, ERP systems integrate it as a standard, and it provides an immediate production plan. In stable or low-variability environments, this approach could be functional. However, in more complex, changing contexts or those with significant physical constraints, it becomes a source of error and operational frustration.
Finite Capacity: Modern Planning Aligned with Operational Reality
Finite capacity planning introduces a realistic and detailed view of available resources. Each production order is validated against the actual capacity of work centres, considering:
• Cycle times and setup times
• Defined shifts and schedules
• Operator availability
• Maintenance schedules
• Priorities and sequencing rules
This allows for a feasible plan, without overloading lines and respecting existing constraints. It also enables scenario simulation: What happens if an extra shift is added? What if a priority order is expedited? How does the plan behave if a machine breaks down?
Key Differences Between Finite Capacity and Infinite Capacity
Choosing between finite or infinite capacity planning isn’t just a technical decision; it involves adopting a specific management and planning philosophy. Both approaches make different assumptions and generate very different consequences for daily operations. Understanding these differences is essential for making sound decisions that affect production plan effectiveness, compliance levels, and responsiveness to actual demand. Below, we examine the key aspects that distinguish them.
Approach and Assumptions
• Infinite Capacity: Assumes that production can always meet demand, regardless of the required resources.
• Finite Capacity: Recognises that resources are limited and must be prioritised and sequenced.
Impact on the Production Plan
• Infinite Capacity: Produces plans that, while theoretically complete, cannot be executed as presented.
• Finite Capacity: Produces executable plans that respect time, resources, and constraints.
Compliance Level and Reliability
• Infinite Capacity: Generates delivery promises that are often unmet.
• Finite Capacity: Allows plans to be met and improves OTIF (On Time In Full) indicators.
Relationship with Actual Demand
• Infinite Capacity: Reacts to demand without considering plant capacity.
• Finite Capacity: Balances demand with resources, anticipates limitations, and adjusts workloads based on these restrictions.
When to Apply Finite Capacity and When to Apply Infinite Capacity
There is no one-size-fits-all planning model for all companies. The decision between working with finite or infinite capacity should be based on an analysis of multiple operational, strategic, and technological factors. Let’s explore the main criteria to help determine which approach is more suitable for each organisation.
Industry or Product Type
The industry in which the company operates strongly influences the capacity planning model choice. In industries with high-value products, complex processes, or strict regulatory compliance (such as pharma, automotive, aerospace, or food), finite capacity is almost essential to ensure precision, traceability, and compliance.
On the other hand, sectors with standard products, stable cycles, or low customisation may temporarily operate with infinite capacity, especially if the planning is complemented with buffers and operational margins.
Degree of Demand Variability
When demand is highly fluctuating, seasonal, or uncertain, planning with finite capacity allows for more agile responses and anticipation of operational limitations. This approach favours scenario simulation, prioritisation of critical orders, and dynamic resource management.
In contrast, if demand is linear, predictable, and low-risk, an infinite capacity model, properly adjusted with rules and restrictions, may provide acceptable results in less demanding environments.
Level of Automation and Process Maturity
Companies with advanced processes, automated lines, and formalised planning structures are better equipped to implement and maintain finite capacity models, maximising their granularity. This approach requires discipline in master data, real-time time control, and operational visibility.
In organisations with lower maturity, where processes are still manual or informal, an infinite capacity approach may serve as a transitional solution until a more solid organisational structure is achieved.
Availability of Digital Tools
Without the right tools, reliably applying finite capacity can become a complex and non-scalable manual task. The key is to have a digital solution that allows for modelling constraints, calculating real workloads, and automatically re-planning in case of changes.
If the company lacks specialised technology or continues to work only with spreadsheets or basic ERPs, infinite capacity will be the only viable option. Transitioning to finite capacity necessarily requires the digitalisation of the planning process.
Finite Capacity or Infinite Capacity? Consequences of Choosing the Wrong Planning Approach
Adopting an unsuitable planning model not only affects the theoretical plan but also triggers a series of operational consequences that affect the entire supply chain. When unrealistic assumptions are made (like those in infinite capacity), deviations soon appear: missed delivery dates, collapsed production lines, unbalanced inventories, and a progressive loss of coordination between departments. Below, we analyse the most common effects of disconnected planning.
Delivery Delays
Using infinite capacity can lead to promising delivery dates that are impossible to meet. This negatively impacts customer satisfaction and company reputation.
Overloaded Lines and Teams
An unrealistic plan creates overloads in certain work centres, accumulation of WIP (work in progress), increased lead times, and constant tension on the shop floor.
Unbalanced Inventories
Producing without a realistic sequence leads to premature or incomplete production, resulting in poorly distributed inventories, semi-finished stock, and undeliverable products.
Loss of Trust Between Departments
When the production plan fails, sales, logistics, and purchasing departments lose trust in planning. This fuels disorganisation, over-purchasing, and constant emergencies.
The Role of SCM Software in Finite Capacity Planning
Finite capacity planning requires specialised digital tools that can dynamically manage multiple constraints. SCM software enables modelling and automating this type of advanced planning.
Real Load and Resource Calculation
Such a solution calculates the real load on each resource (machine, line, operator), considering theoretical and actual times, sequences, availability, and scheduled maintenance. This enables visualisation of the impact of each order on the overall load and identifies critical points before execution.
Integration with Demand, Inventory, and Purchases
The production plan cannot stand alone. SCM software integrates demand forecasts, inventory status, and procurement times, creating a connected plan that avoids stockouts, bottlenecks, or overproduction.
Quick Response to Deviations or Restrictions
With an advanced digital solution, it’s possible to simulate scenarios in seconds, automatically re-plan in case of an issue (such as a line stoppage), and prioritise critical orders without losing visibility over the rest of the plan.
Finite Capacity or Infinite Capacity? The Right Choice Can Change Everything
In production planning, working with a realistic foundation makes the difference between executing with precision or constantly improvising. Infinite capacity might seem convenient at first, but its consequences are felt on the shop floor, in inventories, and in customer service.
Adopting finite capacity planning allows for coherent decisions, anticipation of limitations, and the creation of a plan that can be fulfilled. And with SCM software, this transition is possible, scalable, and aligned with each company’s reality.
At Imperia, we offer advanced supply chain planning and optimisation software that creates production plans aligned with your company’s actual capacity. Additionally, with our range of plugins, the tool can be configured according to each client’s specific needs. If you’d like to learn how we can improve your production planning, don’t hesitate to request a free consultation with our experts.
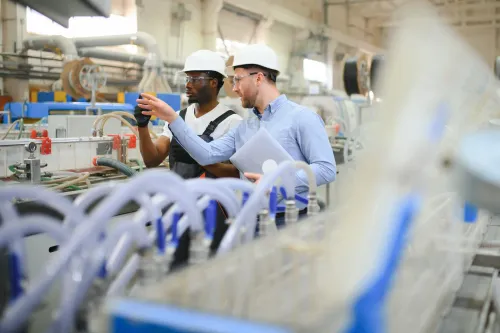
Subscribe to our newsletter and transform your management!
Receive updates and valuable resources that will help you optimise your purchasing and procurement process.