Finite Capacity vs. Infinite Capacity: Which Approach Fits Your Production Strategy?
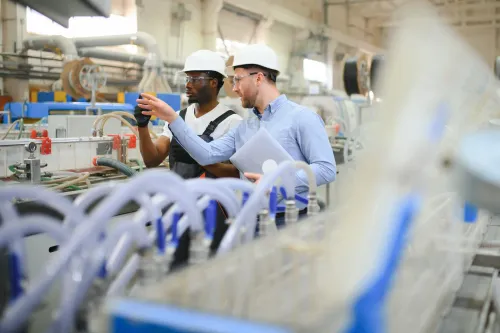
Planning production without factoring in real-world resource limits is one of the main causes of delays, bottlenecks, and execution gaps. Many manufacturers still rely on infinite capacity planning, assuming that machines, people, and facilities can meet any level of demand without constraints. Others have transitioned to finite capacity models that reflect the actual availability of resources and enable more realistic, executable plans.
So, which one should you use? In this post, we compare both approaches, highlight their implications, and explore how SCM software can help you align your production plans with your plant’s true capacity.
What Is Infinite Capacity Planning, and Why Was It So Common?
Infinite capacity planning assumes that production resources (machines, operators, workstations) can absorb any workload, regardless of time or physical limits. Planners input demand, and the system generates a production schedule without verifying if there’s enough capacity to deliver it.
This model was widely adopted for years because it’s quick, standard in most ERP systems, and instantly produces a plan. In stable, low-variability environments, it might suffice. But in dynamic, high-constraint operations, it often leads to unrealistic expectations and inefficiencies.
Finite Capacity: Planning That Matches Reality
Finite capacity planning takes into account the real availability of resources. Each order is scheduled based on:
- Cycle and setup times
- Shift patterns and workforce availability
- Maintenance windows
- Sequencing rules and job priorities
This results in a plan you can execute, one that avoids overloading, respects real-time constraints, and enables scenario testing (e.g., What happens if we add a shift? Prioritize a rush order? Or deal with unexpected downtime?).
Key Differences Between Finite Capacity and Infinite Capacity
Choosing between finite and infinite capacity isn’t just about software setting, it’s a mindset. Each approach has different assumptions, outcomes, and impacts on daily operations.
Core Assumptions
- Infinite Capacity: Assumes that production can always keep up with demand, no matter what.
- Finite Capacity: Acknowledges that resources are limited and must be scheduled accordingly.
Impact on Production Plans
- Infinite: Delivers plans that look complete but can’t realistically be executed.
- Finite: Produces accurate schedules that reflect actual constraints.
Delivery Performance
- Infinite: Promises due dates that are often missed.
- Finite: Improves on-time delivery and OTIF (On Time In Full) metrics.
Responsiveness to Demand
- Infinite: Tries to meet demand regardless of operational limits.
- Finite: Balances demand with capacity and adjusts workloads proactively.
When to Use Finite Capacity vs. Infinite Capacity Planning
There’s no universal answer. The right approach depends on your industry, process maturity, and available tools. Here’s how to decide:
Industry Requirements
Sectors like pharma, aerospace, food, or automotive demand precision and compliance, making finite capacity a must. For standard, low-variation environments (e.g., basic packaging or commodity goods), infinite capacity may be temporarily acceptable if buffers are in place.
Demand Volatility
If demand is seasonal, volatile, or promotion-driven, finite capacity helps model disruptions and prioritize orders. In predictable, steady demand environments, infinite planning may work if properly tuned.
Automation and Process Maturity
Advanced manufacturing environments with digital workflows and automated lines are best suited for finite capacity. It requires clean data, disciplined planning, and visibility.
Less mature operations, where planning is still spreadsheet-driven or informal, may need to start with infinite capacity before evolving to a more robust system.
Digital Infrastructure
Finite capacity relies on digital tools that can calculate workloads, simulate constraints, and dynamically replan. Without a capable SCM platform, maintaining finite capacity manually is slow, error-prone, and unsustainable.
If your business doesn’t yet have the right tech stack, infinite planning may be the only feasible option until digital transformation is underway.
What Happens When the Wrong Model Is Used?
Choosing an unsuitable planning model doesn’t just hurt scheduling, it creates a ripple effect across the supply chain. Over-promising, operational chaos, and broken coordination are all symptoms of disconnected planning.
Missed Delivery Dates
Overpromising based on infinite capacity can lead to missed deadlines, hurting service levels and customer trust.
Line Overloads and Production Stress
Unrealistic plans overload machines and teams, increase WIP, and cause bottlenecks on the shop floor.
Inventory Imbalances
Plans that ignore sequencing create mismatched inventory: early runs of unneeded parts, incomplete assemblies, or undeliverable finished goods.
Departmental Friction
When production can’t deliver what was promised, sales, procurement, and logistics lose trust in the plan, causing misalignment, over-purchasing, and firefighting.
How SCM Software Powers Finite Capacity Planning
Finite capacity planning only works at scale with the right digital tools. Advanced SCM platforms enable:
Real-Time Load Calculation
Software calculates actual resource load per line, operator, or machine, based on availability, sequences, shifts, and planned downtime. You can visualize pressure points before they disrupt execution.
Integrated Planning Across Functions
The production plan connects with demand forecasts, inventory levels, and procurement lead times, creating a synchronized, end-to-end view.
Fast Response to Changes
Scenario planning lets you test «what-if» scenarios instantly, adjust for line stoppages, and prioritize urgent orders, without losing control over the rest of the schedule.
Make the Right Call: Finite Capacity or Infinite Capacity?
In production planning, realism wins. Infinite capacity might seem faster, but it rarely delivers when reality kicks in. Finite capacity ensures that your schedules are grounded in what’s truly possible.
With the right SCM tools, the transition to finite capacity becomes scalable, sustainable, and tailored to your organization’s needs.
At Imperia, our supply chain planning platform helps manufacturers build production plans that match actual capacity, enhanced by powerful plugins that adapt to your process.
Ready to optimize your planning? Book a free consultation with our experts and discover how to bring capacity-based planning to life.
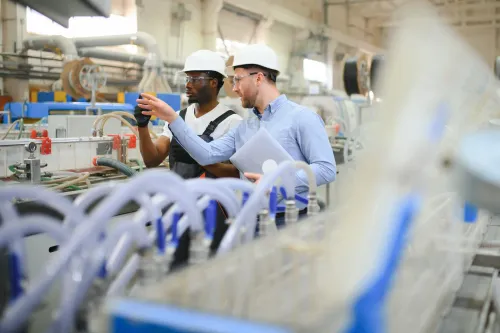
Subscribe to our newsletter and transform your management!
Receive updates and valuable resources that will help you optimize your purchasing and procurement process.