Lean Manufacturing and Its Impact on Production Planning Efficiency
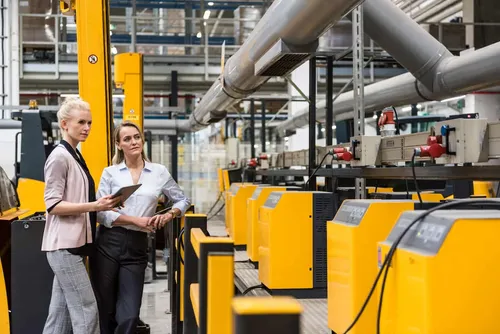
Lean Manufacturing has revolutionized the way companies manage their production processes. Its focus on waste elimination and continuous improvement not only optimizes operational efficiency but also transforms production planning into a more agile and effective function. In this article, we will explore how Lean Manufacturing impacts the efficiency of production planning by analyzing its principles, tools, and benefits.
1. Introduction to Lean Manufacturing
Lean Manufacturing, or lean production, is a philosophy that seeks to maximize customer value while minimizing waste. This methodology originated from Toyota’s production system and has been adopted across various industries to improve efficiency and quality.
1.1 Fundamental Principles of Lean
The five fundamental principles of Lean are:
- Define value: Understand what the customer considers valuable.
- Identify the value stream: Map all activities that contribute to the final product.
- Eliminate waste: Recognize and remove activities that do not add value.
- Create continuous flow: Ensure that products flow uninterrupted through the production process.
- Establish a pull system: Produce only what is needed, when it is needed.
2. Waste in Production
Waste is any activity that consumes resources but does not add value to the final product. Lean Manufacturing identifies seven main types of waste:
- Overproduction: Producing more than what the customer demands.
- Waiting: Time lost waiting for materials, equipment, or decisions.
- Transportation: Unnecessary movement of products or materials.
- Excess processing: Doing more work than necessary to meet customer requirements.
- Inventory: Holding more materials than needed.
- Motion: Unnecessary movements by employees.
- Defects: Products that do not meet quality standards.
3. Impact of Lean Manufacturing on Production Planning
3.1 Improved Visibility and Control
One of the primary ways Lean Manufacturing enhances production planning is through improved visibility and control. By mapping the value stream, companies can identify bottlenecks and areas for improvement. This enables planners to anticipate issues and adjust production schedules accordingly.
3.2 Flexibility in Planning
Lean Manufacturing promotes flexibility in production planning. Instead of following a rigid schedule, companies can quickly adapt to changes in customer demand. This is achieved by implementing pull production systems, where products are manufactured based on actual demand, reducing overproduction and excess inventory.
3.3 Enhanced Collaboration
The Lean philosophy fosters collaboration among departments, which is essential for efficient production planning. By encouraging communication between sales, production, and logistics teams, companies can better align with customer needs and optimize production accordingly.
4. Lean Tools for Production Planning
Lean Manufacturing provides various tools that can facilitate production planning. Some of the most effective include:
4.1 Just-In-Time (JIT)
The Just-In-Time (JIT) system focuses on producing only what is needed, when it is needed. This not only reduces inventory costs but also minimizes the risk of overproduction. JIT planning requires close collaboration with suppliers to ensure that materials arrive just in time.
4.2 Kanban
Kanban is a visual tool that helps manage workflow. It uses cards to indicate when a product or material needs to be replenished. This allows production teams to have a clear view of the production status and facilitates decision-making.
4.3 Value Stream Mapping (VSM)
Value Stream Mapping (VSM) is a technique that helps identify and analyze the flow of materials and information through the production process. By visualizing the flow, companies can identify waste and areas for improvement, allowing for more effective planning.
5. Benefits of Implementing Lean in Production Planning
5.1 Cost Reduction
Implementing Lean Manufacturing in production planning can lead to significant cost reductions. By eliminating waste and optimizing resource use, companies can operate more efficiently and profitably.
5.2 Quality Improvement
Lean Manufacturing also contributes to improving product quality. By focusing on defect elimination and continuous improvement, companies can deliver products that meet customer quality standards.
5.3 Increased Customer Satisfaction
The ability to quickly adapt to customer demands and deliver high-quality products results in increased customer satisfaction. Companies that implement Lean Manufacturing tend to have more loyal and satisfied customers, leading to increased sales and profitability.
6. Challenges in Implementing Lean Manufacturing
6.1 Resistance to Change
One of the biggest challenges in implementing Lean Manufacturing is resistance to change. Employees may be accustomed to established processes and may be reluctant to adopt new practices. It is essential to involve all staff in the change process and provide the necessary training.
6.2 Commitment from Top Management
Top management commitment is crucial for the success of Lean implementation. Without support and participation from organizational leaders, it is difficult to establish a Lean culture and ensure that initiatives are sustainable in the long term.
6.3 Need for Continuous Training
Continuous training is essential to maintain the Lean philosophy within the organization. This includes training on Lean tools, continuous improvement techniques, and skill development for employees. Without proper training, employees may revert to old habits and processes.
7. Success Stories in Lean Manufacturing Implementation
7.1 Toyota
Toyota is the pioneer in implementing Lean Manufacturing. Its production system is an example of how waste elimination and continuous improvement can lead to greater efficiency and quality. The company has managed to reduce costs and improve customer satisfaction through Lean practices.
7.2 Boeing
Boeing has utilized Lean principles to optimize its production process. The company implemented techniques such as value stream mapping and Just-In-Time to improve efficiency in aircraft manufacturing. As a result, Boeing has reduced production time and improved product quality.
8. Conclusion
Lean Manufacturing is a powerful methodology that significantly impacts the efficiency of production planning. By focusing on waste elimination, continuous improvement, and collaboration, companies can optimize their production processes and better adapt to market demands. Although implementing Lean may present challenges, the benefits in terms of cost reduction, quality improvement, and increased customer satisfaction are invaluable. Adopting Lean Manufacturing not only transforms production but also establishes a solid foundation for sustainable growth in the future.
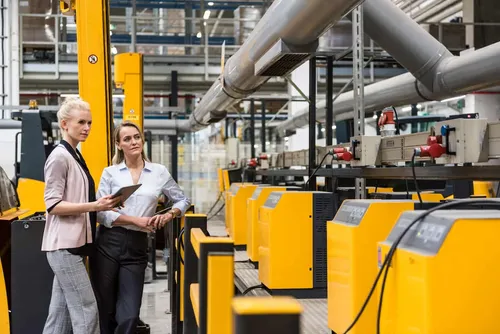
Subscribe to our newsletter and transform your management!
Receive updates and valuable resources that will help you optimize your purchasing and procurement process.