Reducing Inventory to Reveal Operational Weaknesses Across Your Supply Chain
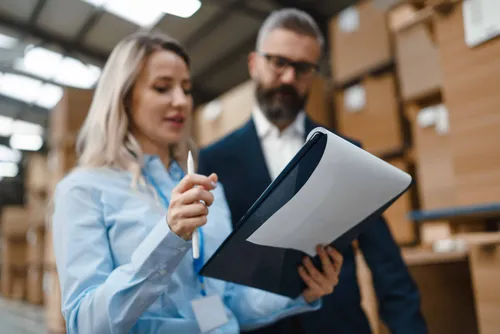
Cost control, operational efficiency, and service performance are key drivers of competitiveness in today’s supply chains. That’s why effective inventory management is no longer optional, it’s a critical piece of any successful supply chain strategy. Yet many companies still carry excess inventory without asking what inefficiencies might be hiding beneath the surface. Reducing inventory helps to detect these problems and apply solutions to improve operational efficiency.
This is where the analogy of “lowering the water to reveal the rocks” offers a fresh perspective. It challenges the traditional mindset around safety stock and encourages a more proactive approach to uncovering hidden issues and driving operational improvement.
In this article, we’ll break down what the concept means, how to apply it safely, the benefits it can unlock, and why SCM software is essential to maximize results without unnecessary risk.
What Does “Lowering the Water” Mean for Inventory Management?
This visual analogy compares inventory levels to the water level of a river: the higher the water, the harder it is to see the rocks underneath. Translated to supply chain terms, the more inventory you hold, the harder it is to detect inefficiencies buried in your operations. These «rocks» could be anything from quality defects or supplier delays to manual errors or siloed communication.
When inventory is reduced, those hidden problems start to surface. What was once absorbed by surplus stock becomes visible forcing the organization to address root causes. Far from being a risk, this exposure creates an opportunity for lasting process improvements.
Common Issues Hidden by Excess Inventory
Here are some frequent issues that often stay unnoticed due to high inventory buffers:
- Inbound and outbound warehouse errors that are masked by overstock.
- Unreliable supplier deliveries that are offset by excess inventory.
- Poor product turnover leading to waste or obsolescence.
- Undetected quality issues, thanks to available backups.
- Inefficient picking or replenishment processes hidden by surplus.
The Real Goal of Reducing Inventory
The goal isn’t to cut inventory at random, but to intentionally reveal underlying inefficiencies. It’s not an endpoint, a method to optimize performance across the supply chain by making problems visible and solvable.
Reducing Inventory in a Controlled Way
To apply this strategy successfully, inventory must be reduced gradually and strategically, backed by data, KPIs, and digital tools. The goal isn’t to empty the warehouse but to reach the point where weaknesses in your processes begin to show. Agility and visibility are critical to avoid service disruptions or stockouts.
Exposing Deeper Operational Issues
As inventory is scaled back, core problems begin to emerge from demand planning inaccuracies to flawed master data. This transparency enables teams to focus on what matters, deploy resources more effectively, and drive real improvement based on actual data, not guesswork.
Operational Benefits of This Approach
When done right, this method creates value across logistics, planning, supplier relations, and beyond.
Driving Process Efficiency
Identifying bottlenecks and weak spots allows you to redesign workflows for speed and accuracy. From goods receipt to replenishment, every step can be streamlined using real-world insights.
Cutting Costs and Improving Quality
Lowering inventory reduces storage needs, cuts obsolescence risk, and frees up working capital. And by bringing quality issues to the surface, teams can fix them and raise standards across the board.
Improving Supplier Performance
Once delays or compliance issues become visible, companies can take action whether it’s renegotiating terms, switching providers, or putting tighter controls in place. The result: a more dependable supply chain.
Case Study: How TecnoAgro Transformed Its Operations by Reducing Inventory
To illustrate how this works in practice, let’s look at a fictional example of TecnoAgro, a company that optimized its performance by applying this strategy.
Starting Point: TecnoAgro in 2023
TecnoAgro, a distributor of farming equipment, maintained high inventory levels to ensure instant availability. While this supported service levels, it also led to high logistics costs, slow inventory turnover, and overall inefficiency.
The Shift in 2024
In 2024, TecnoAgro’s leadership rolled out a new inventory management system and began reducing stock levels gradually. The strategy was guided by KPIs and supported by a digital platform to track every transaction. Within just a few months, long-hidden issues became visible:
- Irregular shipments from global suppliers
- Defective batches of spare parts
- Discrepancies between system data and actual inventory
Taking Action
With those issues now on the radar, TecnoAgro acted quickly:
- Renegotiated key supplier contracts
- Adopted RFID tracking and routine cycle counts
- Reorganized critical SKUs into more efficient storage locations
- Improved master data accuracy and demand forecasting
Measurable Impact
As a result, the company achieved:
- A 38% reduction in storage costs
- A 17% increase in service level for high-priority parts
- A 21% cut in replenishment lead times
- A drop in return rates due to quality issues, from 5.8% to 2.1%
Beyond inventory optimization, the company also strengthened supplier relationships, improved service delivery, and became more competitive.
How SCM Software Helps to Reducing Inventory
Reducing inventory without the right tools in place can backfire. That’s why an SCM platform is critical. It provides the structure, data, and control needed to execute this strategy effectively.
Real-Time Inventory and Demand Insights
With full integration across purchasing, sales, and warehouse operations, Supply Chain Management software delivers a single source of truth. This visibility supports smarter decisions, proactive replenishment, and demand-aligned inventory levels.
Automation and Intelligent Replenishment
Built-in algorithms respond to real-time data, usage patterns, and supplier lead times. This reduces manual work, minimizes the risk of overstocking, and ensures each item is kept at the optimal level.
Quality, Traceability, and Compliance
A modern SCM system tracks incidents, logs every batch, and generates audit-ready reports essential for industries like pharma, food, or automotive, where compliance is non-negotiable.
Reducing Inventory as a Driver of Visibility, Control, and Optimization
This isn’t just another inventory tactic, it’s a mindset shift toward transparency, continuous improvement, and smart decision-making. By revealing what’s really going on beneath the surface, businesses can fix what’s broken, improve how they work, and build a more resilient supply chain.
To make it work, the right technology is non-negotiable. SCM software not only supports this strategy, it transforms it into a long-term competitive edge.
At Imperia, we help businesses digitize and optimize every supply chain process.
Our modular platform adapts to your needs and gives you only the features that matter most. Want to see what it could do for you? Request a free consultation with one of our experts, we’d love to help.
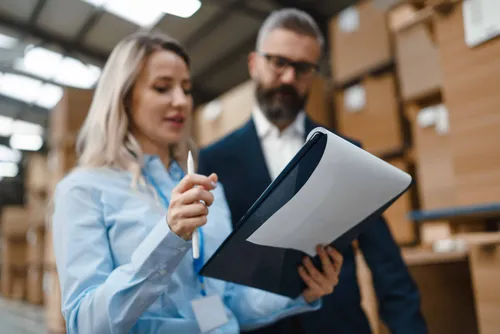
Subscribe to our newsletter and transform your management!
Receive updates and valuable resources that will help you optimize your purchasing and procurement process.