Aggregate Planning: A Tactical Approach to Staying Ahead in the Supply Chain
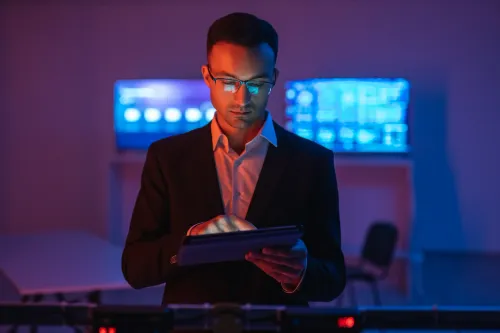
In supply chain management, focusing only on short-term execution often leads to reactive decisions, production bottlenecks, or inventory imbalances. Companies operating with a mid-range horizon need tools that help them project future scenarios, allocate resources efficiently, and develop structured responses to demand shifts. Aggregate planning is designed to meet that need.
This planning layer covers a time frame of roughly 3 to 18 months and provides a consolidated view that helps align decisions across demand, production, procurement, logistics, and capacity. It plays a central role in the S&OP process. In this article, we’ll explore what aggregate planning is, its objectives, the variables it involves, and how to apply it effectively.
What Is Aggregate Planning?
Aggregate planning is a mid-term planning method that translates a company’s strategic goals into actionable operational plans. It determines, over a defined period, the volume to produce, the capacity required, and the inventory levels to maintain. Rather than working at the SKU level, it operates at a higher level of aggregation, grouping by product families, production centers, or equivalent units.
It acts as a bridge between demand forecasting and the master production schedule (MPS), facilitating a smooth transition from long-term strategy to daily execution.
Key Characteristics of Aggregate Planning
- Time horizon between 3 and 18 months.
- Planning by product family, resources, or equivalent units.
- Fully aligned with the S&OP process.
- Focused on tactical decision-making without drilling down to the SKU level.
Core Objectives of Aggregate Planning
A well-executed aggregate planning strategy helps companies stay proactive, optimize resources, and align cross-functional decisions. Its main objectives include:
Balancing Capacity and Demand
The primary goal is to align production resources with forecasted demand. This involves defining strategic decisions such as:
- When to increase or scale back production.
- When to activate subcontracting.
- How to adjust shifts or introduce overtime.
Maximizing Resource Utilization
Aggregate planning helps distribute workload across production lines, avoid machine overload, and adjust inventory levels to prevent overuse of warehouse space or infrastructure.
Minimizing Operating Costs
By evaluating alternative scenarios (in-house production, subcontracting, stockpiling), planners can identify the most cost-effective option while maintaining required service levels.
Driving Cross-Functional Collaboration
Effective aggregate planning brings together sales, operations, finance, and procurement. It ensures decision-making remains aligned and avoids internal conflicts across departments.
Demand and Capacity: The Two Pillars of Aggregate Planning
One of the strengths of aggregate planning lies in its use of representative variables, offering actionable insights without requiring micro-level detail. These fall into two main categories:
Demand-Related Variables
Forecasted demand is the starting point. Aggregate planning typically considers:
- Product families: Groups of SKUs with similar behavior.
- Seasonality: Demand spikes by period, customer type, or channel.
- External events: Launches, promotions, regulatory changes, etc.
Capacity-Related Variables
Operational capacity is modeled using:
- Internal resources: Shifts, labor calendars, maintenance, etc.
- Equivalent units: Standardized output to support planning.
- External capacity: Subcontractors, secondary suppliers.
- Logistics constraints: Available storage, transportation limits, warehouse access.
Strategies and Tools for Aggregate Planning
To implement robust aggregate planning, businesses must combine a clear operational strategy with analytical tools to simulate and compare scenarios.
Production Strategies
- Chase demand: Flexible but higher cost.
- Level production: Stable but requires buffer stock.
- Hybrid models: Most common, balancing flexibility and efficiency.
Supporting Quantitative Tools
- Total cost models: Help compare trade-offs across scenarios
- Heuristics: Rule-based, practical decision-making tools
- Linear programming: For constraint-based optimization
The Forecast’s Role in Aggregate Planning
Forecast accuracy is critical to the success of aggregate planning. Estimates must be regularly updated and reflect reality at the product family level. Poor forecasting leads to:
- Oversized production plans.
- Unnecessary logistics expenses.
- Capacity overloads and missed deadlines.
Practical Example: Applying Aggregate Planning
Imagine a company with two product families: A and B. The demand forecast for the next quarter is:
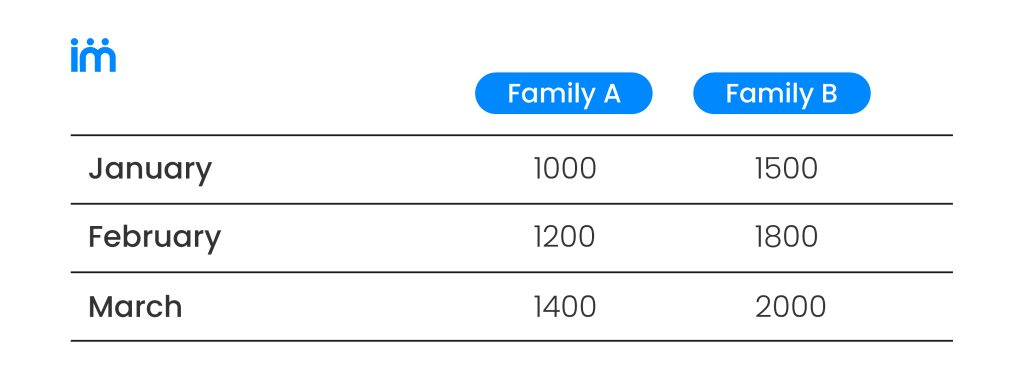
Let’s say total monthly capacity is capped at 2,000 units. Given the imbalance in projected demand, the team must decide whether to:
- Subcontract some of the production
- Build inventory in January to cover March
- Modify work schedules or introduce overtime
The best solution depends on the cost of each option. This type of analysis can be quickly automated using advanced supply chain planning software.
Tangible Benefits of Aggregate Planning
When implemented effectively, aggregate planning delivers real operational and financial gains:
- Lower overall operating costs.
- Smarter use of installed capacity.
- A more stable master production schedule.
- Improved customer service levels.
- Better alignment across departments.
From Forecast to Action: Why Aggregate Planning Matters
Aggregate planning is more than a monthly volume estimate. It transforms business goals into realistic, coordinated operational actions. It’s a flexible, collaborative tool that helps companies anticipate change, reduce risk, and operate with greater consistency over the mid-term.
With the right SCP solution, companies can embed aggregate planning into day-to-day operations, simulating scenarios, connecting forecasts to procurement, and aligning teams across functions.
Ready to take control of your planning? Book a free consultation with our experts and learn how to turn forecasting into a competitive advantage.
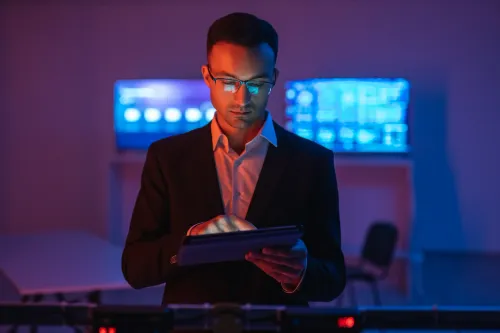
Subscribe to our newsletter and transform your management!
Receive updates and valuable resources that will help you optimize your purchasing and procurement process.