How to Identify and Eliminate Bottlenecks in the Supply Chain
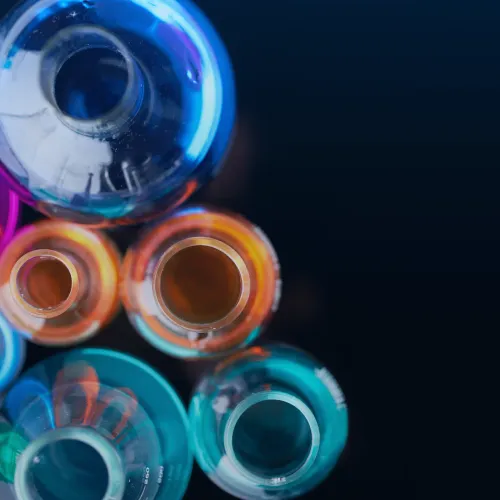
The supply chain serves as the backbone of any enterprise, but bottlenecks can disrupt its smooth operation and hinder performance. Strategic decision-makers play a critical role in ensuring operational efficiency and customer satisfaction.
This article explores the concept of bottlenecks in the supply chain, providing insights on how leaders can identify these critical constraints and implement effective strategies to address their impact and enhance overall operational efficiency. Furthermore, it highlights the importance of using advanced analytical tools, such as the «bottleneck calculator,» to optimise operations efficiently.
What Are Bottlenecks in the Supply Chain?
A bottleneck in the supply chain refers to a point or process that constrains the overall system’s capacity to function efficiently. This can lead to production delays, inventory management issues or distribution challenges. Bottlenecks can arise in any part of the supply chain.
Examples include sluggish assembly lines, imbalanced inventories and delayed decision-making processes. Identifying these issues is the first step towards ensuring that processes achieve the desired performance levels.
Four Key Steps to Identify and Overcome Bottlenecks
In a conventional batch-and-queue system, Steps 1 and 2 can quickly generate an excess inventory that accumulates at Step 3, turning it into a bottleneck. Consequently, Steps 4 and 5 come to a halt, awaiting the completion of Step 3.
1. Identification – Comprehensive Process Analysis
Initiating the optimisation process involves conducting a capacity analysis for each process, covering everything from raw material acquisition to the final delivery of the product or service. This approach enables precise identification of critical points where waiting times accumulate, resources are utilised inefficiently or deviations from deadlines occur.
The table demonstrates that optimising Steps 1 and 2 results in a greater accumulation of items before Step 3. Similarly, increasing the speed of Step 5 yields limited benefit if Step 3 cannot supply inputs at the necessary rate. This highlights the importance of pinpointing individuals or machines that are consistently at full capacity, particularly those with significant work backlogs, as they are the most likely sources of bottlenecks.
2. Exploitation – Optimising Bottleneck Performance
Once the bottleneck is identified, it is crucial to ensure its optimal performance, as «an hour lost at the bottleneck is an hour lost for the entire system.» To achieve this, it is recommended to safeguard the bottleneck by placing inventory buffers that guarantee a constant supply of materials. This ensures that, even if upstream disruptions occur, the bottleneck remains continuously engaged.
Additionally, it is vital to minimise time losses by avoiding idleness and reducing downtime or quality errors. Recommended actions include implementing parallel preparation processes, preventive maintenance and conducting quality checks at earlier stages. These measures help to maximise the bottleneck’s efficiency and support the smooth flow of operations throughout the system.
3. Subordination
Steps 1 and 2 should operate at a pace that generates a workload manageable by the bottleneck.
This principle aligns closely with the «Drum–Buffer–Rope» methodology which is designed to ensure that the bottleneck consistently operates at full capacity.
- Drum: This component of the strategy involves making the bottleneck, or the critical step, operate at the maximum possible pace. This aligns with the idea of enhancing performance in the key area of the supply chain to maximise overall efficiency.
- Buffer: This involves introducing strategically placed inventory buffers. These buffers act as shock absorbers, protecting the bottleneck from variability in supply or unexpected delays, and helping to maintain a continuous, stable flow.
Through careful inventory management and strategic buffer placement, organisations can avoid both overproduction and underutilisation. This supports a balanced, predictable flow of materials, minimises unplanned downtime and sustains optimal performance at the constraint.
4. Elevation – Increasing Bottleneck Capacity
Exploring ways to expand the system capacity may include introducing faster machinery or increasing automation at the bottleneck stage.
Alternatively, capacity constraints can be alleviated by redistributing resources across processes.
Strategies to Eliminate Bottlenecks
Predictive Data Analysis
This strategy entails applying predictive analytics to anticipate future events in the supply chain. By collecting and analysing historical data, as well as external variables, the company can forecast seasonal patterns, demand shifts, and other key factors.
Access to these insights enables proactive decision-making, allowing businesses to adjust operations in advance. This helps prevent the overuse or underutilisation of resources, stabilises production planning and enhances overall supply chain resilience.
Intelligent Automation
Intelligent automation involves the deployment of advanced technologies, such as robotics, machine learning and autonomous systems, to perform specific tasks without constant human intervention. By applying this strategy, companies can eliminate bottlenecks by enhancing speed and accuracy in critical processes.
Interdepartmental Collaboration
Collaborative efforts across teams enable the sharing of critical information and decision-making that benefits the entire value chain. This strategy helps eliminate bottlenecks by ensuring a smoother supply chain and more accurate planning.
For instance, collaboration between production and procurement teams ensures that materials are available when needed, preventing delays and disruptions on the production line.
Production Flexibility
The production flexibility strategy focuses on the ability to quickly adapt to demand changes by adopting modular lines. This allows the company to efficiently switch between different products without compromising operational efficiency.
By enabling rapid reconfiguration of machinery and workflows, production flexibility optimises resource utilisation and enables the company to navigate market dynamics, eliminating potential bottlenecks.
The Importance of Calculating Bottlenecks
Calculating bottlenecks has become a priority for supply chain professionals.
The bottleneck calculator is a powerful tool that assists supply chain professionals in assessing the efficiency of their operations. This tool utilises real-time data and advanced algorithms to identify specific areas where capacity might be compromised.
By adopting this technology, leaders can anticipate potential issues and develop strategies before issues escalate, ensuring a more resilient and responsive supply chain.
At Imperia, we draw on the insights and feedback of experienced industry professionals to continuously enhance our solutions. If you seek support in identifying potential critical points in your supply chain and/or improving your planning processes, we would be delighted to assist you free of charge. Feel free to contact our Supply Chain experts and select the day and time that suits you best.
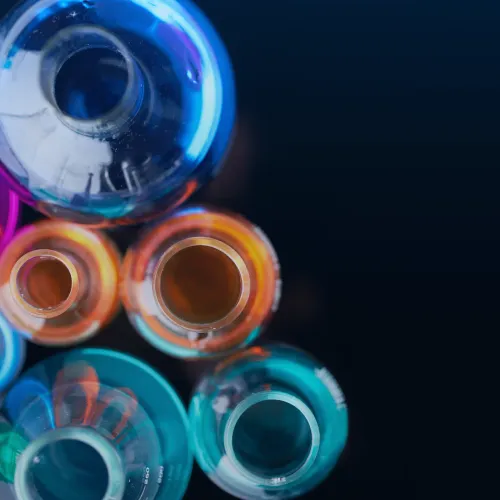
Subscribe to our newsletter and transform your management!
Receive updates and valuable resources that will help you optimise your purchasing and procurement process.